
NIMBLE is an advanced robotic system revolutionising the warehouse automation industry, allowing companies to build and implement efficient robotic systems. It is based on imitation learning-based artificial intelligence, which allows it to imitate human operators within a warehouse.
With this technology, robots can be trained to move and manipulate objects within a warehouse with minimal human supervision. In this article, we’ll discuss the technology behind NIMBLE and how it can develop imitation learning-based warehouse robotic systems.
Overview of NIMBLE robotic system
The NIMBLE robotic system is a mobile platform designed to enable the collection, transport, and analysis of data for various applications. This innovative robotic system manoeuvres through tight spaces and unpredictable terrain with ease. It’s equipped with a wide range of sensors, including LIDAR, cameras, and sonar, allowing it to detect its surroundings and map its environment in real time. Additionally, NIMBLE offers customizable software packages suited to each customer’s needs so that data collected can be processed accordingly.
The mobility component of the platform is powered by powerful motors controlled by precise cadence control algorithms. It can navigate steep inclines, stairs, and slippery surfaces like polished concrete or carpeting. It also features seven degrees of freedom (DoF), allowing it to take on a variety of body orientations for greater manoeuvrability in tight spaces. Its lightweight reusable structure also allows for reduced fatigue during transport between locations.
NIMBLE comes equipped with an array of high-end sensing technologies such as LIDAR sensing that can create 3D point clouds to detect objects like walls or furniture within its vicinity. In addition, its RGB cameras allow for a visual representation of any environment mapped by the system enabling safe navigation for mission-critical autonomous applications such as search & rescue operations or warehouse material tracking tasks. All these sensors are integrated into NIMBLE’s on-board computing unit which gives it access to high performance machine learning frameworks that facilitate object recognition & pose estimation tasks vital for carrying out complex robotic operations or data analytics capture missions successfully by reducing false positives and minimising response time errors associated with cloud computation latency losses during transmission between server units at different geographical locations.
How it Works
The Nimble robotic system is a warehouse robotic system based on imitation learning that allows for autonomy. This robotic system can learn from its environment and use this data to adapt and perform tasks with minimal human intervention.
Let’s take a look at how the Nimble robotic system works.
Imitation Learning
Imitation learning is a machine learning concept used by the NIMBLE robot arm to teach itself how to do a task through observation. This allows the robot to learn tasks in a safe and interactive environment for humans.
At its core, imitation learning is based on a particular approach called “Observe & Replicate” which involves the robot watching humans perform an activity then attempting to replicate their actions. First, the NIMBLE system will observe human demonstrators performing tasks with the robotic arm using its onboard camera system. Then, it will use artificial intelligence (AI) algorithms to recognize and map out various elements of what it observed—including body movements and tool placement—to replicate these movements at different levels of precision.
Using this technique, the NIMBLE robotic system can quickly imitate complex motions without prior knowledge of the action being demonstrated or challenging programming skills required by human operators. Furthermore, with each practice run, the advanced AI algorithms improve accuracy and repeatability, further refining its performance until it has mastered the desired task.
Overview of Imitation Learning
Imitation Learning (IL) is a branch of Artificial Intelligence (AI) that studies how machines and robots can learn a task by observing how humans or other machines do it. It utilises techniques from Machine Learning, Computer Vision, and Robotics to understand how an action is performed and then re-creates it most efficiently. A robotic system using IL follows four sequential steps: Observation, Representation, Execution and Adaptation.
Observation: The robot system starts with no knowledge about the task. Therefore, it must observe the action being demonstrated by humans or machines to obtain an initial understanding of the task. This is commonly done by recording detailed visual images of the movement in 2D (2-dimensional) or 3D(3-dimensional) contexts.
Representation: In this step, observation data must be converted into understandable terms so that the robot can perform it independently. For example, suppose we are teaching a robot to throw a ball. In that case, we need to convert the data into parameters such as force intensity, elbow angle/position etc., which can be used as instructions to complete the particular task.
Execution: After all these preparation steps have been taken care of, it’s time for the robot to replicate what was observed by performing its actions based on learned parameters read previously in Representation stage and execute them sequentially to complete its goal for a particular situation/task. To maximise efficiency and accuracy, the NIMBLE robotic system relies on supervised learning techniques where robots are given feedback from external sources like humans or sensor devices afterwards once they act on their performance so that they can learn from mistakes and develop better strategies next time when a similar situation arises again.
Adaptation: As environment condition or scene changes over time due to external effects such as lighting intensity or other mechanisms acting upon environment; Robots using IL systems need adaptive strategy which allows them with capabilities to change their trained models accordingly depending on external conditions so that they can always achieve highest possible degree of accuracy under any circumstances given those conditions do not contradict with rules pre-specified during training phase of robot beforehand itself.
Advantages of Imitation Learning
Imitation learning (also known as apprenticeship learning) is a strategy for robotics that enables robots to learn from the actions of humans and other exemplary problem-solvers. This type of learning has several distinct advantages.
Firstly, teaching a robot by imitation can be easier than programming it from scratch in a robotic language such as ROS (Robot Operating System). This can save time and effort as the robot can learn from its environment more quickly than trying to program it with specific instructions. Secondly, imitation learning can be particularly useful for applications where the task is complex or when no computer program exists for the chosen task. Likewise, if a job or task requires fine motor control and accuracy, then robotics technology has difficulty emulating this skill through programming instruction only. Imitation learning mitigates this issue by allowing machines to perform tasks they would not otherwise be able to do.
Another advantage of imitation learning is safety—interaction with minimal damage within an unpredictable environment. By duplicating human behaviour safely and accurately, robots can work in environments where people or animals cannot go or need added protection due mainly to dangerous environments such as high radioactive radiation levels found in nuclear facilities or on disaster sites like Chernobyl’s premises.
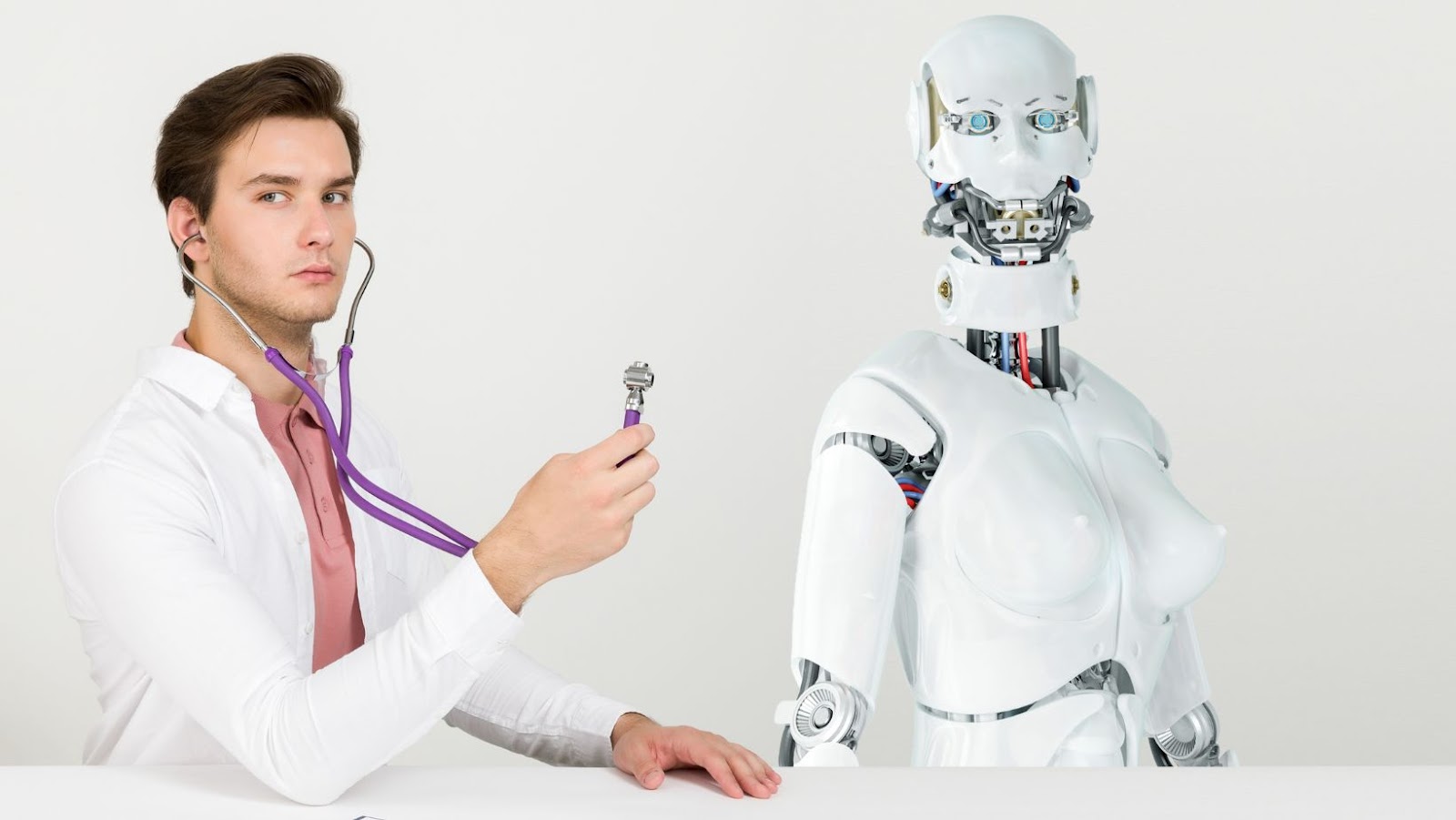
Warehouse Robotics
Warehouse robotics are automated solutions for various tasks in a warehouse setting. These solutions have become increasingly popular given the efficiency and cost savings they can offer. The NIMBLE robotic system is a great example of this, utilising advanced computer vision, machine learning, and artificial intelligence algorithms to automate many common warehouse operations such as material handling and sorting.
The NIMBLE system relies on sensors to detect and identify items in the warehouse environment, allowing it to accurately locate items within seconds. This allows for improved speed, accuracy and flexibility compared to manual labour operations. In addition, NIMBLE robots use sophisticated manipulators (driven by robotic arms) capable of picking up items of different sizes and weights with impressive precision.
Overall, the NIMBLE robotic system is a powerful tool that helps warehouses achieve greater operational efficiency while optimising labour costs. With its fast response times, effective material identification technology and safe operating principles, this automation platform can provide many advantages over traditional manual warehouse operation methods.
Overview of Warehouse Robotics
Warehouse robotics streamline and automate the process of handling goods, materials and inventory through robots that can autonomously navigate the warehouse environment. Through automation technology, these robots can improve stock accuracy, reduce labour costs and solve problems related to global supply chains.
Robots like those found in the NIMBLE robotic system use an array of sensors including colour cameras, depth cameras, encoders and more to understand the layout and objects of their environment. With the help of this sensing equipment, robots can measure distance, recognize items with 3D models stored in memory and store positioning information for navigation purposes.
Robotics automation systems use several kinds of navigation methods to plot their movements within a facility:
– Holonomic Navigation: This approach involves simultaneously controlling all degrees of motion to accurately move between two specific points. Robots that use holonomic navigation rely on multiple motors, allowing them to quickly find solutions for complex manoeuvres like rotating around an object or spiralling around a wall.
– Obstacle Avoidance: This method uses low-level capabilities such as line following or rotary sensing to analyse the environment from a basic perspective to detect obstacles and avoid them safely during transport.
– SLAM Navigation: By relying on advanced algorithms and learning techniques, robots using SLAM navigation can map their environment as they move by creating internal models that accurately track obstacles and other features within their workspace. This allows them to navigate different pathways without getting lost or stuck between multiple objects while moving.

Advantages of Warehouse Robotics
Robots are increasingly being utilised in warehouses to increase productivity, reduce human error and lower operational costs. Warehouse robotics systems use the latest in sensing, monitoring and control technology to automate traditional processes and create close-to-perfect conditions of operational accuracy. NIMBLE is a robotic system that uses multi robot coexisting architecture for real-time coordination and control.
The primary advantages of warehouse robotics systems like NIMBLE include increased efficiency through automated sorting, improved safety by reducing the need for workers on the production line, space savings due to incoming packages being stored in less space than manual operations would require, decreased environmental impact from both package transport and waste reduction from higher accuracy picking, faster order completion cycles to meet customer demands quickly and accurately while reducing overall costs.
In addition to the primary advantages is the potential for warehouse managers to better monitor inventory levels to adjust production ordering more accurately without risking stock outages.
NIMBLE’s Robotic System
NIMBLE is a robotic system developed by the company of the same name. This system was developed to help warehouse operations become more efficient. It uses imitation learning based on images and videos of humans performing tasks. This enables it to learn the task quicker, with fewer resources and a lower cost.
This article will examine how NIMBLE’s robotic system works and how it can benefit warehouse operations.
Components of the System
NIMBLE is an autonomous robotic system designed to be used in various contexts. It consists of two main components: a robot controller and multiple robots, such as ground-based and/or aerial drones. The robot is controlled by its on-board software and remote commands from the robot controller.
Robot Controller: This is the command centre for the system, issuing commands and monitoring state information for each robot. It also keeps track of tasks and shows overall system status information.
Ground Robots: These are four-wheeled ground robots equipped with sensors, motors, cameras, lidar (Light Detection And Ranging) systems and payloads to execute various tasks autonomously or via remote control. They have multiple modes so they can move through indoor or outdoor environments at different speeds or settings per the user’s choice.
Aerial Drones: These quadcopter drones allow navigation in three dimensions, via height adjustment and tilting forward or backward while flying long distances in horizontal paths. They feature high resolution cameras which produce live video feed for streaming and object tracking tasks, along with advanced image processing algorithms built into them for object detection. Additionally, they come equipped with GPS, barometer-based obstacle avoidance technology and infrared range finders for precise navigation around obstacles like trees or buildings during flight missions.

How the System Works
NIMBLE is a collaborative robotic system designed to automate virtually any process. It combines robotics technology with artificial intelligence and advanced computer vision to understand and intuitively interact with its environment, making it ideal for various applications.
The main components of NIMBLE are the robot arm, the controller, and the software stack. The robot arm is designed to be open-source, meaning anyone can develop or modify it according to their needs — from basic projects to custom industrial tasks. This makes it easy to adapt NIMBLE to different tasks and environments.
The controller is an advanced electronic device that acts as the “brain” of the system. Using algorithms developed with machine learning techniques, the controller controls the movements of each motor to achieve the desired outcome, such as manipulation tasks or navigation through an environment. In addition, it relies on computer vision algorithms that enable it to recognize objects and surroundings within its field of view.
Finally, NIMBLE runs on a modular software stack that integrates all components to execute complex operations and provide data logging capabilities while keeping power consumption levels low. This stack consists of low-level control (robot control tasks), middleware (communication between components) and high-level application programming interfaces that take care of user interface development so users require no code writing.
NIMBLE ROBOTIC DEVELOPS IMITATION LEARNING-BASED WAREHOUSE ROBOTIC SYSTEMS
NIMBLE Robotics has developed a groundbreaking imitation learning-based robotic system for warehouses. This system allows robots to quickly and accurately perform various tasks and has many advantages over traditional methods.
This system is a great solution for automating warehouses and can significantly improve efficiency and productivity.
Let’s take a closer look at the benefits of NIMBLE’s robotic system.
Increased Efficiency
NIMBLE’s Robotic system helps businesses increase efficiency and automate manual processes. With the ability to streamline complex tasks, robotic systems can enable businesses to reduce administrative costs, improve accuracy and quality of work, and increase productivity.
In addition, utilising robotic systems helps minimise employee fatigue and reduces the chances of human errors occurring during production or other processes.
Robotic systems can quickly perform tasks that require extensive labour from multiple people. This increases output speed and accuracy while freeing up resources for more value-added activities. Robots are more precise than humans in various operations such as dispensing liquids or moving parts from one place to another; therefore ensuring quality control is kept in check with minimal manpower needed. In addition, NIMBLE’s Robotic system can be programmed to carry out various tasks without direct human supervision, allowing staff members to focus on other responsibilities.
Robotic systems can also provide increased safety in hazardous working environments such as high noise levels, extreme heat, or cold. NIMBLE’s Robotic system offers protection from physical dangers while minimising risk by using advanced sensors that detect changes in environment conditions during operation. Furthermore, routine maintenance procedures are easier to complete with robust robots requiring fewer repairs over time due its robust design and long-lasting components.
Cost Savings
As a smart and cost-efficient automation solution, NIMBLE’s robotic system creates cost savings through increased productivity and reduced labour costs. The robotic system can increase efficiency, accuracy, and speed by automating processes while reducing manual labour costs.
Additionally, the NIMBLE robotic system enables organisations to benefit from a lower total cost of ownership compared to other automation investments. The system also allows for scalability due to its modular design and ability to be integrated with existing systems.
Further cost savings come from predictive maintenance features that can detect issues with equipment before they become costly problems. Through improved cycle times, data capture capabilities, fewer errors and improved quality control, the NIMBLE robotic system has several measurable benefits that make it an effective investment for companies looking to increase efficiency while still controlling costs.
Improved Safety
Using NIMBLE’s robotic system allows organisations to improve safety by having robots perform tasks that would be dangerous to a human worker. These robots are programmed with advanced intelligence, able to respond and adjust to changing conditions. As a result, robots can easily handle hazardous or highly technical tasks, reduce operator fatigue, and help avoid manual handling of materials or tools that could put workers at risk of injury.
The NIMBLE robot system is designed for safety—each robot is constantly monitored by sensors that register nearby objects’ location and motion. This ensures safe collaboration between robots, personnel, and other stationary objects in the workspace. In addition, the robots operate in an enclosed environment surrounded by perimeter guards that evaluate the vicinity and restrict access when any obstacle lies near their path. Having these sensors on board the robotic arm coupled with fail-safe brakes makes it easy to ensure safe working conditions for people in the surrounding environment.
These intelligent machines can also communicate with one another wirelessly or through structured cabling networks, avoiding any onboard monitoring systems from being tampered with manually. Therefore, workers have peace of mind knowing no matter what’s happening around them, they’re always protected from accidents or injuries caused by a vulnerable robot arm colliding into its workspace surroundings.
tags = announced a $50 million Series A financing led by DNS Capital, accelerate the company’s hiring plans, product and technology development and scaling of robot deployments for its customers’ fulfillment operations, nimble series feifei li thrunheatertechcrunch, robotics feifei li thrunheatertechcrunch, series feifei sebastian thrunheatertechcrunch